SPECIAL REPORT: How tech is increasing palm oil production in Nigeria
Nigeria’s estimated annual palm oil consumption is 2.4 million tons. Yet, the country has a deficit of 0.9 million tons of palm oil. The major drawbacks are the use of climbers for harvesting and local mill to extract palm oil.
But with the introduction of harvesting technologies and improved palm oil extractors, there has been an increase in palm oil production. Kelechukwu Iruoma traveled to four Niger Delta states and reports on how these technologies are improving palm oil production in Nigeria.
On a sunny Tuesday afternoon, two women in their 30s were on a moving motorcycle along Ubulu-Uku — Isselu-Uku road in Delta state. One, fair in complexion was riding while the other — dark in complexion was seated on the passenger seat carrying a five-year-old girl.
As they approached the palm oil farm of Kingsley Ojeah, who was using a harvesting tool — a Mechanical Adjustable Harvester (MAH) — to prune palm bunches from the trees, the motorcyclist stopped. Their banter drew the attention of Ojeah, who stopped pruning.
“Is there a machine that is used to prune palm fruits from the trees?” One of them asked Ojeah, who replied in affirmation.
In Ubulu-Uku and many parts of Nigeria, where people engage in palm oil production, climbers are mostly used to prune palm fruits. The women had never seen MAH technology before. The way Ojeah was pruning palm bunches within seconds amazed them.
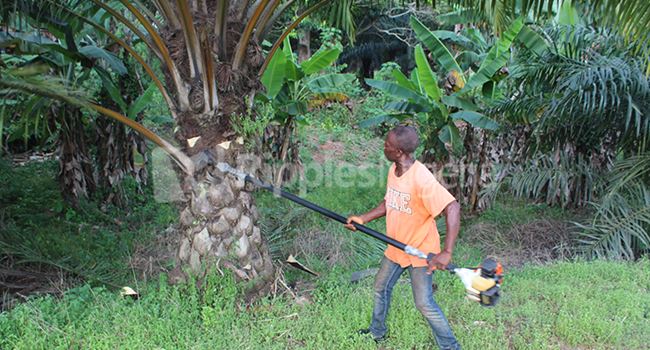
Kingsley Ojeah pruning bunches with his mechanical adjustable harvester at his farm in Ubule-Uku in Delta state
‘50% of bunches are wasted by climbers in the course of pruning’
Harvesting palm fruits can be time-consuming and labour-intensive as the traditional varieties of palm oil trees are tall, prompting the need for climbers. About 60% of smallholder plantations in the Niger Delta region — the major producer of palm oil in Nigeria— are above seven meters tall, making the task expensive and dangerous.
In the past, Ojeah used to employ climbers to harvest and prune for him. He said the use of climbers does not produce the desired results. “Sometimes, the fruits will ripe and spoil on the trees. When you call climbers to harvest, they will keep postponing and before you know it, the fruits get spoilt. But with the use of the MAH, I prune myself without climbers,” said Ojeah.
“Before now, we were involved in manual means of harvesting using cutlasses and for trees that are taller; we use the rope to climb to be able to access the palm fruits for harvesting,” says Osagie Melody, the Chief Executive Officer of Lixomon palm oil farms.
But he said there are risks associated with the use of climbers, adding that some climbers have lost their lives in the course and some have broken legs. “There are times climbers fall from the trees when using rope”, he stated.
Climbers are scarce, and becoming more expensive and as a result, a large amount of fruits are lost as they rot on the trees. Harvesting palm trees’ Fresh Fruit Bunches (FFB) is one of the major constraints of the oil palm industry in Nigeria as 50% of bunches are wasted by climbers in the course of pruning.
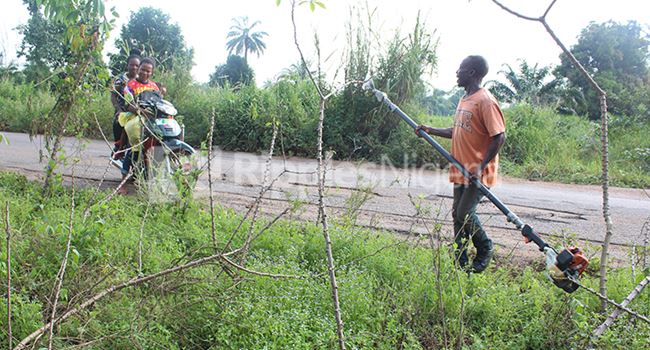
Two women stop to ask Kingsley Ojeah on the use of MAH to prune
“One thing about palm is that if you leave the bunches there without harvesting them, you are damaging the palm,” says Festus Fyalakwe, an oil palm farmer, who uses another tech harvester, Malaysian Knife.
“We had the challenge of snake biting while climbing to harvest. We run when we see a snake. As a result, we fail to harvest. Also, during the raining season, it is difficult to climb the trees because they are slippery. The challenges of climbing are much.”
Moses Monday also uses the Malaysian Knife. He had worked with PRESCO Plc and the Nigeria Institute for oil Palm Research (NIFOR) and has been an oil palm harvester for 15 years. He used to climb but he stopped because of the risk associated with it. “The challenge of climbing is falling and one can get bitten by a snake. That is what I am afraid of.”
Due to these underlying challenges, oil palm farmers lose so many palm bunches. While some of them get rot after being abandoned, others are not well harvested.
Nigeria’s palm oil sector not meeting production demands
In the 1960s, Nigeria was the leading producer of palm oil. Now fourth globally, accounting for 3% of global production, it meets domestic demands through imports. The Niger Delta region accounts for roughly 57% of the palm oil produced in Nigeria. According to research, over 1,400 metric tons of palm oil was consumed in 2017.
Considering Nigeria’s population of about 200million and per capita consumption of 12.5 Kg per person per annum against the world average of about 20 Kg per person per annum, estimated annual consumption is 2.4 million tons. Hence, Nigeria has a deficit of 0.9 million tons of palm oil worth more than USD 800 million.
Palm oil farmers complain that whenever they use the services of climbers, they have many palm fruits losses. “There are trees that have low areas. When you use manual [climbers], it will be difficult to harvest fruits in those areas and it takes more days,” said Ruth Nwangba.
“Climbing is difficult. One of my climbers cut his leg in the process of killing a snake he saw on the tree while harvesting,” continued Nwangba.
Fyalakwe harvests every two weeks. With the use of climbers, he finds it difficult to meet his targets. He was introduced to the technology and since then, “I harvest every two weeks and I maintain the frequency. But without a Malaysian knife, it may last for two months and all the palms will be getting rotten”, he said.
“Two weeks frequency is the best for every palm plantation and with the use of the Malaysian knife, it makes the work quicker and faster. Other farmers should learn how to use the knife. The knife cuts into pieces any snake that it comes across in the course of harvesting. I don’t even climb while using the knife, I stand and harvest,” he continued.
Malaysian knife and mechanical adjustable harvesters to the rescue
A non-governmental organization, Foundation for Partnership Initiatives in the Niger Delta (PIND), introduced the MAH and the Malaysian knife to palm oil farmers across the Niger Delta, eliminating the need for climbers.
“Even a blind man can see it. It takes just five minutes to prune one tree when using a climber but in five minutes, I can prune up to ten palm trees with the use of the mechanical harvester easily,” says Ojeah.
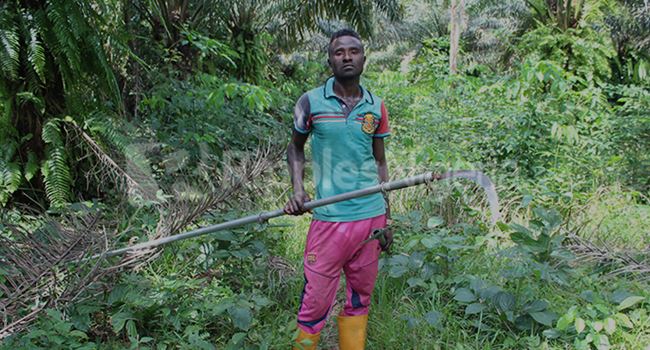
Festus Fyalakwe holding his Malaysian Knife after pruning
“As I am talking to you, I am happy because, throughout this year, I didn’t lack, my farm is always filled with bunches. If I tell you the jerry cans of oil I sold this year, I made good money. Initially, I get 80 cans every year but this year [2018], I got 180,” he continued.
Ojeah said he has been able to buy more hectares of land to plant extra 500 palm fruit trees as a result of the bumper harvest he got in 2018.
With the MAH, harvesting job has been made a lot easier, says Melody. “By using the machine, one man can conveniently do the job of four persons. The job you ought to have done for four days you can complete it in one day by using the same workforce.”
Melody, who has four MAHs said that for his workers to harvest palm bunches in tall trees, they do not require rope to climb because the MAH allows them to harvest from the ground because it has the capability of harvesting from 25ft from the ground and the tendency of falling from the trees is drastically reduced.
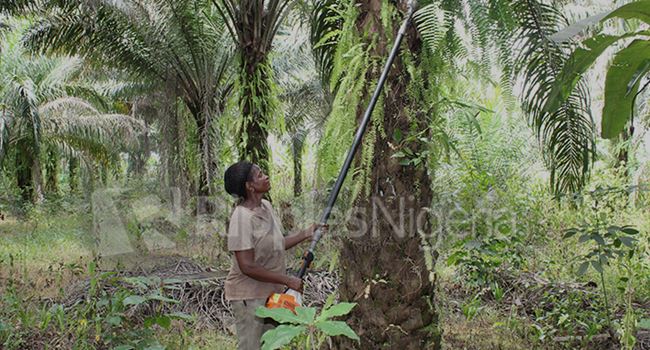
Ruth Nwangba using the MAH technology to prune at her farm in Benin
Increased production and income
Nwangba said the MAH is economical and does not consume too much fuel. “With one litre of fuel, you can harvest a whole farm of five hectares. It has reduced my stress in the oil palm production and I get double of what I get now using the MAH and it has increased my income.”
“A situation where a climber wants to climb a tree to harvest the fruits in a tree, the Malaysian knife must have pruned more than 10 trees. If a climber with a rope can get 100 bunches a day, someone who is using the Malaysian knife can harvest 300 bunches a day,” says Fylakwe.
He said with the use of the Malaysian knife, a harvester can harvest around 1,000 trees a day while a climber with a rope can only harvest 100 bunches a day.
Monday who is a harvester trained at Okomu Oil Palm Company said he liked the Malaysian knife. “It is good for me and I understand it. Someone that does not know the knife may not want to use it, but it is better.”
The use of the Malaysian knife has increased his income, says Monday. “Whenever I go to harvest with the Malaysian knife, I must harvest about 1,000 bunches per day. If it is pruning, I can prune 150 palm trees. If I go for work for four days, I don’t go home with anything less than N80,000. That one is an assurance. With climbing, I can’t get that amount”
The MAH costs N280,000 to acquire. But with support from PIND, Ojeah, Nwangba, and others were able to pay half of the amount the technology cost and PIND paid the rest. “This is part of PIND’s efforts to support smallholder farmers across the Niger Delta,” says Nazah Obi-Odu, PIND’s Market Development Advisor on the palm oil intervention.
PIND partnered with NIFOR to train 37 local fabricators to promote the mechanical adjustable harvester and the Malaysian Knife. 57 MAHs and 155 Malaysian knives have been sold to various palm oil farmers across the Niger Delta.
As a result of the harvesting technologies introduced to 1,012 oil palm farmers and harvesters in the region in 2016, Obi-Odu claims it has increased oil palm farmers’ income by N107 million.
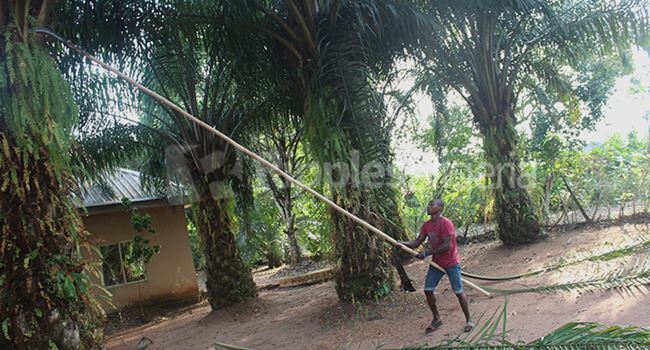
Moses Monday pruning with the Malaysian Knife
She said PIND has increased the availability of the more efficient technology through the sale of over 300 MAH and Malaysian Knives across the Niger Delta and the improvements in management practices. “Access to technology has helped improve the net additional income of over 6,000 benefiting farmers and harvesters to over N1 billion.”
“Harvesting technologies are the best,” says Fyalakwe. “No matter how tall a palm is, the tech harvesters can be used to pick the fruits easily. My advice to people is to stop climbing because it is dangerous.”
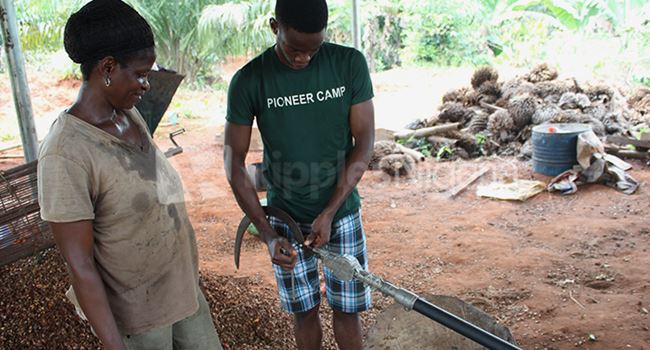
Ruth Nwangba and her son preparing the Mechanical Adjustable Harvester for pruning
Overcoming challenge with the local palm oil extractor
Bola Adetula has been an oil palm processor for 27 years. His palm oil mill is located at Owo, a suburb in Ondo State, one of the Niger Delta states. When he started milling in 1997, he was using the local mill to extract palm oil from palm fruits.
He said what processors were using were manual digester and manual presser, and the means of sterilizing was by burning in drums.
The process involves cooking the palm fruits before it can be digested manually and the means of sterilizing was by burning in drums. Such a process, according to Adetula, is labour intensive, expensive, unhygienic and time-consuming.
Considering the huge demand for palm oil in Nigeria, there needs to be an increase in palm oil production. To meet demands, processors will have to work harder to increase production.
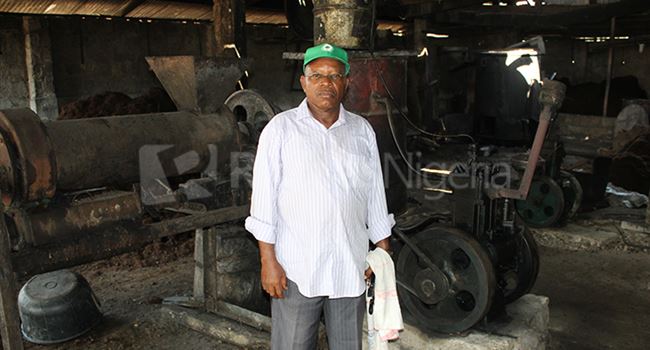
Bola Adetula at his SSPE milling machine in Owo, Ondo state
If Adetula continued with the local mill, he doubted if he could produce quality palm oil and meet industrial demands. “We had milling challenges and we were not getting the best yield from the field. I found out that the local machine could no longer cope with the output of the farm both in efficiency and capacity,” says Adetula.
Stanley Agbaegbu, a processor in Imo with 45 hectares said he used to employ the local mill, but the cost of production was too high. “Sometimes the milling machine would spoil and before we could repair it, the palm bunches will not give us the maximum quantity we need from the oil.”
Dr. Dare Samuel, a palm oil technology expert said in 2012, he carried out a study in Rivers and Imo states and discovered that most of the mills were extracting below expectation.
“As a result, Tenera [a type of palm fruit] that has 21 percent oil content, was able to extract a maximum of 14 percent. And during the mill pressing, they are able to extract, without the machine, about eight percent. For the Dura, which is the improved variety, it contained 12 percent oil content. Without the machine, they extract eight percent from Dura and during the mill season they are able to extract five percent.”
Dare said the oil palm farmers were not following the best management practices to improve yield and maximize profit, adding that it was based on the discoveries that led to the introduction of the new processing machines.
The wonders of improved palm oil extractors
That is the idea behind the introduction of the Small Scale Processing Machine (SSPE) to palm oil farmers, whose extraction rate is 15%. In order to have an unhindered implementation of this intervention, PIND sponsored the training of fabricators in Imo and Edo states in NIFOR.
After the training, the prototype the trainees produced was introduced to palm oil clusters in various states with 50 percent grants. The fabricators started producing for all the mills interested.
Adetula, who resigned his job as a chartered accountant in 2008 to go into full-time palm oil production said the use of the SSPE technology has increased his turnover. “Before we were getting an annual turnover of 100 tonnes per annum from 35 hectares but last year, we got 160 tonnes”
As a facilitator, Dr. Dare organized demonstrations for palm oil farmers to see the performance of the new technology as well as carry out monthly monitoring for those that are using them. Based on the monthly monitoring, from an average of 11 percent, there is an increase to 15 percent extraction rate.
But some trained fabricators went further to fabricate another technology through SSPE called High Capacity Processing Equipment (HCPE) or automated milling machine that has 18% extraction rate. Agbaegbu has now acquired the technology.
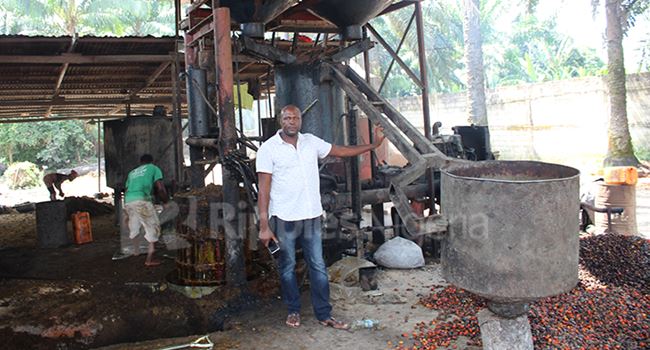
Stanley Agbaegbu at his HPCE milling center in Umuagwo, Imo state
“When we started using the automatic milling machine, it was efficient and we were having high-quality oil and increase in the quantity of oil. We have less cost and labour and easy production,” says Agbaegbu.
But Adetula who is the Chairman of the National Palm Produce Association of Ondo state is hoping to install the new automated milling machine. “The machine is effective because before we decided to go for it, we visited five sites where the machine was installed, we saw it was effective.”
According to Obi-Odu, the introduction of SSPE has made palm oil processors increase profit across the Niger Delta. Processors who used the improved technology now earn a weekly gross profit of N484,667 compared to N255,760 earned by those using the local mills.
Obi-Odu said PIND has sold 114 of SSPE and the automated milling machine, adding that seminars, trainings, and workshops for palm oil farmers, processors and equipment fabricators has reached over 17,000 participants and leveraged over N100 million in investments as at the end of 2017.
“I am expecting to hit 200 tonnes next year because I have been taught many things I did not know,“ says Adetula.